Dymondwood Tips
Tips for Working with Dymondwood®
Turners who attempt to drill Dymondwood with the same techniques they use on
standard wood will often experience problems with overheating and cracked blanks.
A few simple changes in technique will virtually eliminate problems with blowout
and cracked blanks. Turners may also assume that Dymondwood needs the same finishing
techniques that regular woods require. This is not true. Because of the phenolic
resin, Dymondwood can be finished with sanding and polishing only.
Sawing
For pen blanks, leave the section to be drilled about a 1/4" too long. Small chips
on the exit side of the hole can be trimmed away when the section is cut to the
exact length.
When sawing Dymondwood, use fine tooth blades. I find 10 tpi bandsaw blades work
well for this application.
Saw the blank with the layers parallel to the table. If you saw with the layers
perpendicular to the table, there is a good chance the last couple of layers will
chip off near the end cut. This holds true for many types of wood. If you must cut
perpendicular to the grain, use minimal pressure within the last 1/4" of the cut.
Drilling Dymondwood
Place a backup board underneath the Dymondwood blank before drilling. It will reduce
the chance of "blowouts" and cracking when drilling through the end of the blank.
Use a drilling jig that supports the entire length of the blank. If you don't have a
jig that fully supports the blank trying wrapping the blank in tape before drilling.
Electrical tape works well. This technique will provide some support to the blank.
If the blank does crack, the tape will hold chips in place, giving you the
opportunity to repair with CA glue.
Drill Bits
Brad Point, Pilot Point, or Parabolic drill bits are often recommended for drilling
Dymondwood. Standard "jobber" bits are not recommended.
Every bit has its advantages and disadvantages. Brad Point bits are available in
carbide; the big advantage is that you will spend less time sharpening drill bits.
Pilot point bits work very well, but to my knowledge aren't available in carbide. I
have seen parabolic recommended for Dymondwood, but I haven't tried them. I use a
Carbide Brad Point.
Always use very sharp tools. Don't try to get too deep with your cuts. Due to its
hardness and brittleness, Dymondwood can chip or crack. Dymondwood is similar in
drilling properties to Ebony.
Drilling Dymondwood Blanks
Whatever drill bit you use, run your drill at medium to slow speed, keep your drill
bit sharp and use light downward force while drilling.
Back out the drill bit frequently to clear chips and allow the blank to cool. If
excessive heat and force are used, the Dymondwood blank can chip, crack or scorch.
If chips are not cleared excessive side pressures may crack the blank.
If you hear or feel a small "pop" during drilling, you've probably cracked the
blank. This is usually a result of excessive drilling force or compacted chips in
the drill flutes. See Gluing below.
The easiest way to remove heat during drilling is to use water. Drilling speed can
be increased if water is used as a coolant/lubricant. This is my preferred method
for drilling Dymondwood. Water also works great for reducing airborne sawdust and
increases the life of your drill bit.
The technique I use is to squirt water into the hole every few seconds while I
retract the drill bit. Use enough water so that chips come out as slurry. Do not let
the drill bit tip run dry. Drilling speed can be increased substantially by using
this technique. Because this technique is so effective, I would never go back to "dry
drilling."
If you create large amounts of steam (when using water), you know your speed is too
high. All the energy being absorbed by the steam (heat of vaporization) would have
been baking your blank and annealing your drill bit!
Sanding
I find Dymondwood much easier to sand than most regular woods. Since it has very low
water absorption, it wet sands wonderfully.
Wet sand with 120, 220, 320, 600, 1200 grit wet/dry sandpaper.
For a finish that will pass the "Magnifying Glass Test" also wet sand with at least
4000, 8000, 12,000 grit Micro-Mesh™ Cushioned Abrasives.
Polishing
Dymondwood does not require finishes that regular woods required. Because of the
phenolic resin in Dymondwood, it can polish to a very glossy shine without the
application of a finish.
Application of a plastic polish, such as Novus #2, will give you a high-gloss,
luster finish. When properly sanded, the polish does its job in a few passes. For
best results, clean and protect with Novus #1 as a final step.
Gluing
Dymondwood® bonds well with Cyanoacrylate (CA) adhesives and some epoxies.
Small nicks or chips can be repaired by filling with a fine sanding dust from the
same color Dymondwood® and wetting with super thin CA glue.
Hairline cracks repair easily with super thin CA. Allow the CA to wick into the
crack for a few seconds and lightly clamp until dry.
Notes for just for Pen makers
A gap filling adhesive is highly recommended for gluing pen tubes. A foaming
polyurethane glue is a good choice. Many turners like to use thin CA, but we have
heard more reports of cracls and splintering during turning. A gap filling adhesive
doesn't leave un-bonded high spots inside the blank drill hole like thin CA will
often do.
When using a blank end mill, use a cutter slightly smaller in diameter than the
width of the blank. An oversized cutter is much more likely to chip or break the
end of the blank.
Many turners save time by plugging the tube ends before gluing. Some of the
materials I have seen used are Play-Doh and potato. A non-greasy material is
important.
Standard pen blanks are intended for 7mm and 8mm(if you drill straight) holes.
You'll need jumbo blanks for 10mm holes.
Dymondwood® Material properties:
Specific Gravity: 1.15 to 1.3
Density: 0.67 to 0.75 oz per cubic inch
Suggested drill types: Carbide Brad point, Pilot Point, or Parabolic
Suggested glues: Cyanoacrylate (CA)
Caution: Various governmental agencies have identified wood dust as a health
hazard. We always use appropriate safety equipment; we want to remind you to do the
same. If you want to find information on wood dust a good place to start is the
US government OSHA website.
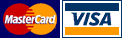
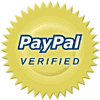
|